Your Guide to Comprehensive Welding Inspection Milwaukee Solutions
Your Guide to Comprehensive Welding Inspection Milwaukee Solutions
Blog Article
How Welding Assessment Contributes to Longevity and Dependability in Fabrication Projects
Welding evaluation serves as a fundamental element in guaranteeing the durability and integrity of construction tasks. By methodically determining potential problems during various stages of manufacturing, welding inspections not only stop expensive failures yet also foster a culture of high quality assurance within the group.

Relevance of Welding Inspection
Ensuring quality via welding inspection is an essential element of any type of fabrication task. It works as a secure to verify that welding procedures satisfy well-known standards and specifications, thereby enhancing the total integrity of the framework or component being produced. Welding examination is not merely a step-by-step action; it is a crucial technique that assists determine prospective issues early, guaranteeing that they are resolved before they escalate into significant troubles.
The value of welding evaluation can be underscored by its function in keeping safety and durability. Welded joints are typically subjected to extreme conditions, and any type of problems can jeopardize the efficiency and longevity of the end product. By applying strenuous examination procedures, companies can make sure conformity with market policies, consequently minimizing dangers related to architectural failures.
Additionally, effective welding evaluation fosters self-confidence among stakeholders, including clients and regulative bodies, that the job meets the best standards. This not just boosts the online reputation of the producer however likewise contributes to long-lasting cost savings by preventing rework and prospective responsibilities. Eventually, welding inspection is important to the success and reliability of manufacture projects, enhancing the value of quality control in engineering methods.
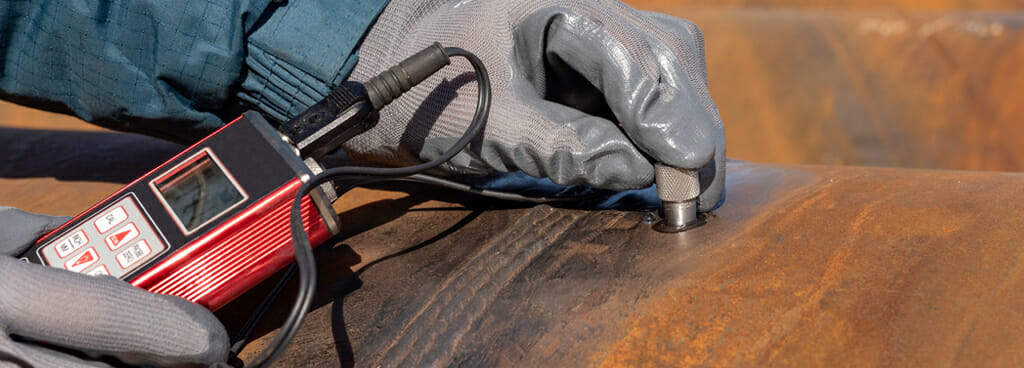
Usual Welding Flaws
Welding issues can substantially weaken the structural stability of produced elements, making their recognition and correction vital. Common welding flaws can be generally classified into three types: geometric, metallurgical, and service-related.
Geometric problems include issues such as damaging, where the base metal is worn down at the edge of the weld, and excessive convexity, which can bring about anxiety focus factors. These defects can compromise the toughness and sturdiness of the weld joint.
Metallurgical problems develop from inappropriate welding procedures or products, resulting in problems such as porosity, where gas pockets form within the weld, and absence of blend, which happens when the weld steel stops working to bond effectively with the base steel. These concerns can considerably damage the weld's efficiency.
Service-related issues might not emerge till after the part is in usage. Examples consist of breaking due to thermal stress and anxiety or exhaustion, which can lead to catastrophic failings otherwise attended to.
Recognizing these usual flaws empowers producers to implement reliable examination techniques that improve the integrity and durability of their tasks, inevitably guaranteeing safety and performance criteria are met.
Evaluation Strategies and Techniques
An extensive strategy to inspection strategies and methods is crucial for mitigating and recognizing welding issues in manufacture jobs. Different approaches are utilized to ensure the honesty of welds, consisting of visual evaluation, ultrasonic testing (UT), radiographic screening (RT), magnetic bit screening (MT), and dye penetrant screening (PT) Each strategy has its toughness and particular applications.
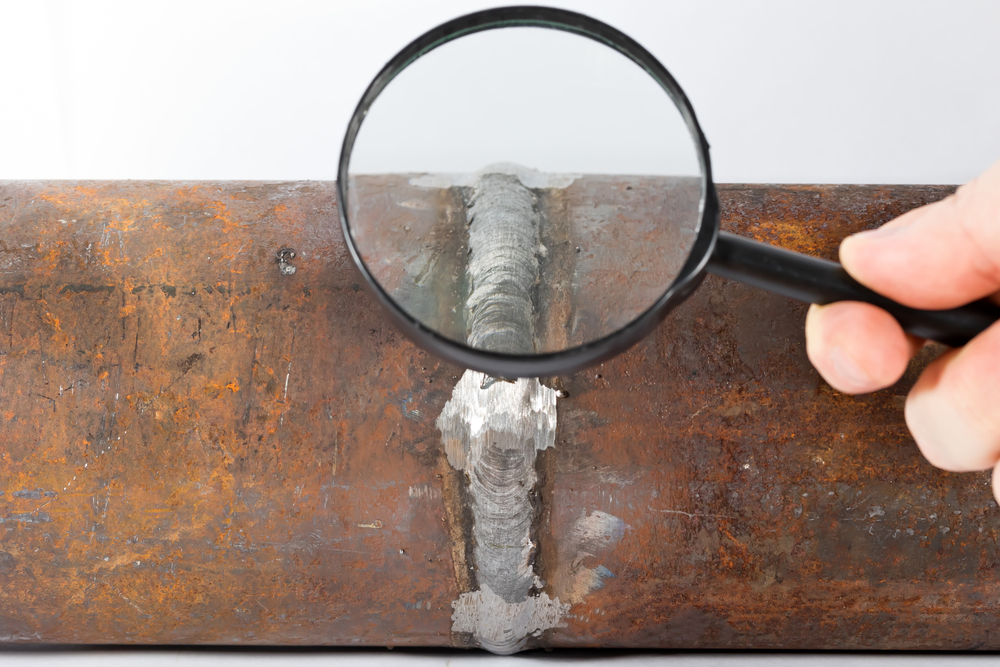
Magnetic bit testing is helpful for identifying surface and near-surface issues in ferromagnetic materials. By applying a magnetic field and making use of ferrous fragments, inspectors can determine discontinuities efficiently. Dye penetrant testing highlights surface-breaking problems through the application of a color that leaks into fractures, making them noticeable under ultraviolet light.
Employing a mix of these approaches ensures a strenuous assessment, boosting the reliability of welded frameworks.
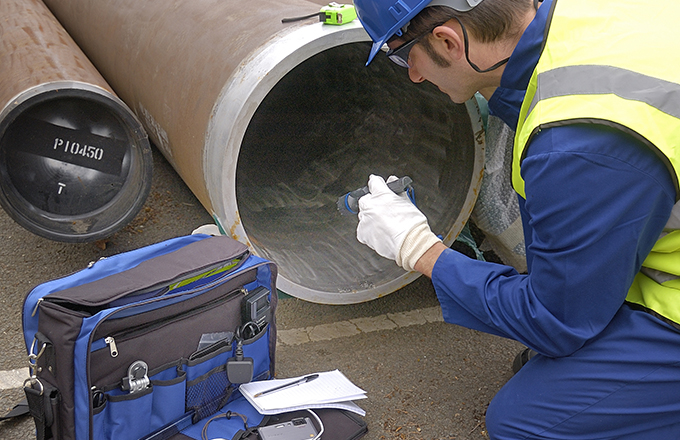
Effect On Task Durability
Reliable evaluation techniques considerably influence the long life of construction projects. By determining potential defects and disparities in welding procedures, inspections ensure that frameworks are developed to withstand functional anxieties with time. When welds are thoroughly examined, the possibility of unseen problems, which could result in architectural failings, is minimized.
Routine assessments help with adherence to sector standards and laws, which are critical for making sure the longevity of bonded joints. Such compliance not just boosts the stability of the job but additionally guarantees stakeholders pertaining to the quality of the work. Prompt discovery of imperfections enables for restorative activities to be taken early, protecting against expensive repair services or complete overhauls down the line. Welding Inspection Milwaukee.
Additionally, reliable evaluation methods promote a culture of quality control within construction teams. When workers know that their job will be rigorously reviewed, they are more probable to stick to finest techniques and preserve high criteria throughout the manufacturing procedure. Ultimately, this commitment to high quality not only expands the life-span of the task but also decreases upkeep costs, thereby boosting the total economic feasibility of look at here fabrication endeavors.
Enhancing Reliability in Fabrication
Dependability in these details manufacture is dramatically boosted with strenuous evaluation processes that resolve possible weak points in welding practices. Reliable welding inspection not just recognizes flaws early yet also gives essential feedback to welders, ensuring adherence to developed standards and specifications. By making use of non-destructive testing techniques, such as radiographic or ultrasonic evaluations, makers can determine the integrity of welds without compromising the material.
Additionally, regular examinations promote a culture of quality and responsibility among fabrication teams. When welders understand that their work undergoes stringent assessments, they are more probable to stick to finest protocols and techniques. This aggressive strategy decreases the risk of costly failings during the functional phase of a job.
In addition, detailed documents of evaluation results produces an important repository of info that can be used for future Related Site projects. Patterns in problems can be assessed to enhance welding strategies and training programs (Welding Inspection Milwaukee). Ultimately, improving dependability in fabrication through extensive evaluation processes not only enhances the life-span of the fabricated components but also reinforces stakeholder confidence in the job's general quality and durability. Investing in robust welding inspection methods is necessary for accomplishing long-lasting integrity in any manufacture venture.
Verdict
In recap, welding evaluation acts as a vital element in guaranteeing the longevity and reliability of fabrication tasks. By identifying flaws early and using non-destructive testing techniques, evaluations foster a culture of quality guarantee that complies with industry standards. The systematic paperwork of outcomes not just assists in pattern analysis yet additionally enhances accountability and structural honesty. Inevitably, efficient welding assessment methods enhance stakeholder self-confidence and dramatically add to the economic stability of manufacture ventures.
Welding inspection serves as a fundamental element in ensuring the longevity and dependability of construction tasks.Guaranteeing top quality via welding evaluation is a crucial element of any fabrication job. Inevitably, welding assessment is indispensable to the success and reliability of fabrication tasks, enhancing the value of quality assurance in engineering methods.
A comprehensive technique to examination techniques and approaches is crucial for reducing and determining welding defects in construction jobs.In recap, welding evaluation offers as a crucial component in making certain the durability and dependability of manufacture jobs.
Report this page